Die Casting Service
Thesun Industry die casting services offer high-output production capacity, low cost, and flexible part design options making it an appealing casting choice for non-ferrous metal products. Our die casting facilities are equipped to handle a variety of designs, materials, and manufacturing needs across multiple industries.
What Is Die Casting?
Die casting is a manufacturing process that produces metal parts by injecting molten metal into a steel mold under high pressure. The metal solidifies to take the shape of the mold, resulting in complex, high-precision parts with excellent surface finish. This method is widely used for non-ferrous metals like aluminum, zinc, and magnesium, and offers advantages such as high production rates and cost-effectiveness for large volume runs. Die casting finds applications in diverse industries, including automotive, aerospace, electronics, and consumer goods.
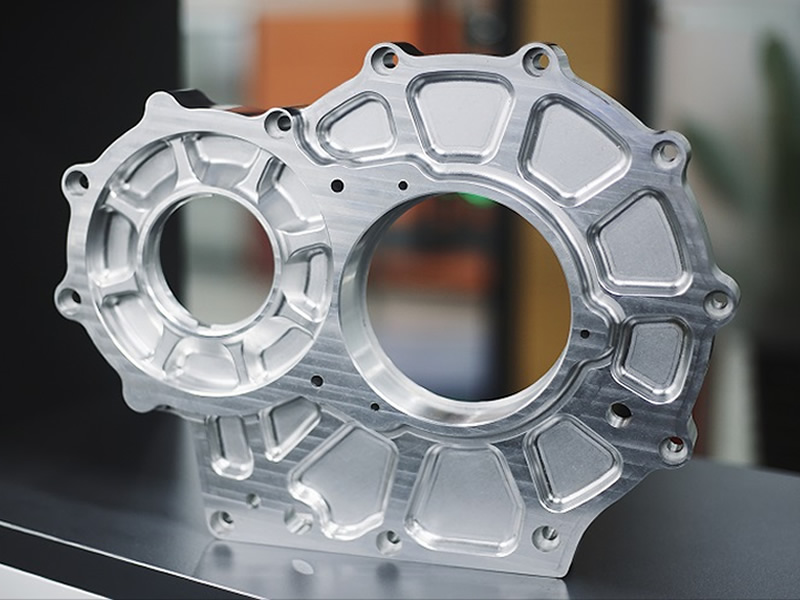
Why Choose Our Die Casting Service?
Extensive Selections
Our die casting services offer a diverse selection of materials, surface finishes, tolerances, and manufacturing processes to suit your specific needs. We provide custom quotes and manufacturing suggestions, ensuring an individualized approach and the most cost-effective solution for your parts.
In house Plant & Facilities
we ensure efficient and fast production of your casting parts. Our state-of-the-art automated facilities enable us to handle a variety of complex customized die casting projects with ease.
Endless Options
Explore countless possibilities with millions of combinations for materials, finishes, tolerances, markings, and certifications for your order.
Strict Quality Control
As an ISO 9001:2015 and IATF16949 certified company, we are dedicated to delivering precision die casting services. Our engineering team at Lingshantech conducts thorough quality inspections at various stages of the manufacturing process, including pre-production, in-production, first article inspection, and before delivery, ensuring the production of the highest quality parts.
Prototyping
Die casting is an affordable and efficient method for creating high-quality prototypes. It utilizes low-cost tooling, making it a cost-effective way to produce prototypes with various materials and design changes.
DVT & PVT Testing
We specialize in creating die casting products ideal for market and consumer testing, concept models, and user evaluation during the Design Validation Testing (DVT) and Production Validation Testing (PVT) stages. Our die casting services enable you to swiftly incorporate changes for thorough performance and dimensional testing before market launch.
Pilot and mass Production
Die cast parts are excellent for custom and first-run production, allowing cost-effective product quality testing before proceeding to full-scale manufacturing. We offer small batch and large-scale production services, accompanied by PPAP (Production Part Approval Process) documentation for quality assurance and validation.
Types of Die Casting We Provide
We collaborate with die casters employing cutting-edge machines and technology to provide top-notch, on-demand parts to diverse industries. Our focus is on two leading types of die casting: hot chamber casting and cold chamber casting. Both methods produce parts with intricate designs, tight tolerances, and strong mechanical properties
Hot Chamber Die Casting
Hot chamber die casting, also known as gooseneck casting, is a die casting process used to manufacture high-precision, high-efficiency metal parts. It is particularly suitable for the production of small and medium-sized parts with complex shapes and thin walls. The process is mainly used for casting metals with low melting points, such as zinc, magnesium and some lead-based alloys. Hot chamber die casting is widely used in the manufacturing industry, especially for the production of small and medium-sized parts for a variety of applications, including automotive parts, electronic housings and consumer products.
Cold Chamber Die Casting
Cold chamber die casting is a process in which the chamber is kept at room temperature, the metal is individually melted in a furnace, and then the metal is poured into the chamber by hand. Unlike hot chamber casting, it does not use a plunger system; instead, a stamping press presses the molten metal into the mold under high pressure. This method is ideal for materials with high melting temperatures, such as aluminum, magnesium, copper and ferrous alloys. The process reduces heat and corrosion problems in machine parts, making it critical in certain applications. It is used in various industries such as automotive, aerospace and electronics.
Material
Aluminum Alloys
Aluminum alloys are one of the most commonly used materials for die casting. They possess excellent mechanical properties, outstanding corrosion resistance, and low density, making them suitable for a wide range of applications, such as automotive parts, aerospace components, electronic enclosures, and more.
Some of the other common characteristics of cast aluminum alloys are:
- Lightweight
- High Strength
- Excellent Thermal Conductivity
- Corrosion Resistance
- High Machinability
- Recyclable
- Precision Manufacturing of Complex Parts
ThesunIndustry offers the most popular aluminum die casting alloys:
- A360.0
- A380.0
- A383.0 (ADC12)
- A413.0
Zinc Alloys
Zinc alloys are extensively used in the die casting process for various applications.Their excellent casting properties make them a preferred choice for producing intricate and high-precision parts across diverse industries including automotive parts, electrical and electronic components, furniture hardware, consumer goods, communication equipment, industrial equipment, and medical devices.
Zinc is an all-around well-performing material due to its balance of mechanical and physical characteristics, which include:
- Impact strength
- High hardness
- Great stability
- High-quality surface finish and easily plated
- Low melting point
ThesunIndustry offers the most popular types of Zamak and ZA die casting zinc alloys. More specifically, those alloys include:
- Zamak 2 (ZA-2)
- Zamak 3 (ZA-3)
- Zamak-5
- Zamak-7
- ZA-8
- ZA-12
- ZA-27
Available Die Casting Surface Finishes
Standard (As-Cast):
Zinc and aluminum-zinc parts can be left as-cast, providing reasonable corrosion resistance. However, aluminum parts require coating for corrosion resistance. Cast parts may have rough marks at the gate locations where they were broken away from the casting sprue, as well as visible marks from ejector pins. The surface finish for as-cast zinc alloys is typically 16-64 microinch Ra, achieved without high-end tools or machinery.
Bead Blasted:
Bead Blasting is a process that uses compressed air to spray fine glass beads onto the surface of die casting parts, resulting in a smooth, matte appearance. This technique changes the appearance or shape of the part and provides excellent cleaning and surface preparation for secondary finishing operations.
Powder Coating:
All die cast parts can be powder coated, which involves electrostatically spraying powdered paint onto the part and baking it in an oven. This process creates a durable, wear- and corrosion-resistant layer, with a wide variety of colors available for the desired aesthetic. Powder coating can be applied to zinc and aluminum alloy die casting, uniformly adsorbing the powder to mask defects effectively.
Plating:
Die cast parts can undergo various plating processes, including electroless nickel, nickel, brass, tin, chrome, chromate, Teflon, silver, and gold plating. Electroplating serves functional, decorative, or corrosion-related purposes and is widely used in industries such as automotive, where chrome-plating of steel automobile parts is common.
Anodizing:
Anodizing is mainly used for aluminum alloy die casting. It generates a layer of aluminum oxide (Al2O3) film on the surface of parts, providing high insulation and wear resistance. Type II anodizing creates a corrosion-resistant finish, while Type III offers a thicker, wear-resistant layer in addition to corrosion resistance. Anodized coatings are not electrically conductive and are typically not used for cosmetic finishes on die cast parts.
Chemical Film:
Chromate conversion coats can be applied by suppliers to protect aluminum from corrosion and enhance the adhesion of paints and primers. These chemical film conversion coatings are electrically conductive.
Advantages of Die Casting
Complex Geometry
Die casting is capable of producing custom parts with thin walls and intricate geometry that are durable and maintain dimensional stability.
Strength
Metal die castings are known for their superior strength compared to plastic injection molded parts and their ability to withstand high temperatures. Materials like aluminum, in particular, offer exceptional strength-to-weight ratios.
Precision
Die casting provides standard tolerances ranging from +/-0.003″ – 0.005″ per inch but can achieve tighter tolerances of +/-0.001” depending on your specific requirements, part complexity, and material.
Custom Finishes
Metal finishers have the capability to create cast parts with smooth or textured surfaces, along with various paint and plating finishes. These finishes not only enhance the cosmetic appearance of the parts but also provide protection against corrosion.
Die Casting Applications
Die casting is a perfect ideal for small to medium-sized products with complex features. ThesunIndustry has provided innovative manufacturing solutions for different industrial applications. We offer high quality parts at competitive pricing to value customers in the following industries:
- Commercial & Consumer Products
- Aerospace & Automotive Components
- Connector Housings
- Pumps and Plumbing Fixtures
- Gears
- Appliances and Lighting
- Medical Devices